02-00: Energy characteristics of larger buildings...
Like single-family houses will larger buildings be they apartment houses, office buildings or commercial like shopping centres exhibit a pronounced daily variation in the energy need.
Apartment houses
Though an apartment house in itself constitutes a number of households is the peak need for heat not necessarily equal to the sum of the peak need for heat in the individual households. The reason for this is that chances are that the peak loads in the individual households occur at different times. The total load may hence be reduced using a simultaneity factor defined as
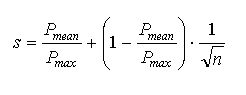
In this equation is Pmean the average heat demanded by a ingle household while Pmax is the peak demand and n is the number of households. Assuming 10 households, each with an average heat consumption of 10 kW and with a peak consumption of 15 kW then yields
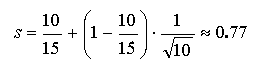
Hence will the peak load with all 10 households become n*Pmax*s = 10*15*0.77 = 116 kW.
Though the short-time peak loads will thus tend to even out will the slower daily variations resulting from social life and working hours sum up. Even if the individual households do not have their morning shower at exactly the same time will they all have their showers at about the same hour of the day.
Office buildings
Office buildings will quite frequently have a pronounced need for cooling during office hours because of the excess
heat delivered by office electronics and by the fact that the number of persons per m2 in an office building is
usually more than the number of people per m2 in homes. The indoor climate in an office building should be adapted to the fact that most people in the building will be sitting most of the day.
Cooling can as pointed out in the introductory chapter 00-01 be produced mainly in two different ways but they will exhibit different cost structures:
• Absorption cooling will take a significant investment cost and becomes most advantageous in cases when the cooling production can be used as a basis for simultaneous production of electricity.
• Compressor cooling produces a lower investment cost while the operational cost becomes higher since it demands electricity as it drive energy.
Hence, for single buildings, compressor cooling will be the main alternative.
Office buildings will frequently have a forced ventilation system which provides for air-borne heating and/or for ventilation heat recovery as part of the heating system.
Commercial buildings and centres
Shopping centres, sports centres, schools, hospitals, official buildings and such, aimed to host a large number of people of varying ages and constitutions and not primarily a cadre of sitting middle-aged people, will again pose new demands on the indoor climate control.
Two main alternatives air-borne or water-borne
Central heating in buildings can be water-borne which is preferred in case of biofuel or it may be air-borne. In case of water-borne heating, the production of tap water is normally integrated in the same boiler but of course with a separate heat exchanger coil. In case of air-borne heating, the production of tap water becomes a completely separate system.
With water-borne systems in larger buildings, where the thermal load may be anything from 50 1000 kW, the water volume in the building heating system will usually be big enough to in itself even out the variations in thermal demand and hence render an accumulator tank unnecessary. With an accumulator tank integrated in the system, though, the integration of solar heating with the system by a separate heat exchanger coil in the accumulator becomes simple.
Since the water volume in the boiler itself or in the combined boiler and accumulator is significant, a water-borne system will provide a thermal inertia that simplifies the control of the system. A sudden increase of the hot water demand, for example, can then be supplied from the stored energy in the system so that the demand can be met while the heat input (for example a pellet burner or in some cases a wood chip boiler) will need some time to get started. The larger the thermal inertia, the longer start-up times may be accepted.
With air-borne heating systems, the thermal inertia is close to zero and the heating system must respond much more rapidly. In larger buildings, where the thermal inertia of the building structure itself is large, can air-borne heating be combined with pellets and with wood chip firing. The supply of hot water, though, will demand separate water heating cirquits.
Different time constants...
With a water-borne system in a large building, the time constant for the water to cool down significantly is measured in single hours. In an apartment house this relatively short time constant may pose problems if the demand for hot water peaks simultaneously in all apartments. Such instances may occur for example during huge sports events when all the families in the house will want to take a shower at the same time ten minutes after the mud-wrestling final.
Hence, water borne systems without an accumulator tank should be combined with primary energy supply systems having short time constants from "off" to full power. For systems firing wood chips, the time from "off" to full power is anything from a few minutes to half an hour depending on the skill of the operator. For modern, automatic pellet burners it is a few minutes. Systems using wood-chips as the fuel should therefore be dimensioned with a larger water volume than is necessary for systems firing pellets.
For air-borne heating systems, the time constant is significantly less than one hour and pellets, gas and electricity are all viable alternatives.
Thus, this again points out the importance to install water-borne central heating in houses intended for biofuel heating.
The control system
The energy system in buildings may sometimes be able to take rather high investment costs. This depends of course on the type of building and the tenants. Opposed to the case in single-family houses, the boiler will typically operate using modulating control.
For office buildings, commercial buildings and other applications that are closed during night, the control system may also include a timer control so that the temperature set points are different between night and day, providing a lower night temperature. The theoretical basis for such a control is outlined in chapter 01-00, but the general conclusion is that the actual effect of a low temperature set point overnight depends strongly on the total thermal inertia of the building. The larger the thermal inertia the lower the effect. Hence will this be an alternative in light, wood structure and wood frame, buildings, while heavy stone buildings will show no or only marginal energy savings by this method. The effect of low night temperature set points on energy saving is enhanced by the use of air-borne heating systems.
Economy of scale
As with any type of heating system; the larger the total heat production becomes, the more dominant becomes the operational (variable) cost. You will see this general aspect outlined in chapter 00-01. In energy consuming applications such as greenhouses will this put a demand on the system to be based on the cheapest (i.e. the most raw) fuel while, in less energy consuming applications like for example a smaller school, a more upgraded fuel such as briquettes or pellets may prove the most economical in the long run.
To optimize the economy it is thus wise to try laying out the system for fuel flexibility. This is, however, possible only within limits:
• A fuel feed system with feeding screws aimed for wood chips may work for briquettes but will typically not work with wood pellets.
• A fuel feed system dimensioned for pellets will in most cases not work with briquettes nor with chips.
• A combustion chamber dimensioned for wet fuels will risk be overheated if fed with a dry fuel.
• A combustion chamber aimed for dry fuels may work with wet fuels but will exhibit inferior environmental performance.
• ...
Planning for fuel flexibility will hence provide the best possibility for a low fuel cost but it will, on the other hand, put high demands on the equipment and will hence increase the investment cost and the costs for the technical consulting during the basic engineering and procurement phases.
To do a thorough economic analysis, the life time of the installation must be estimated and then it becomes important to draw a strict line between, and not confuse, the depreciation time (the economical life-time) and the technical life-time.
The technical life-time of boilers and heating systems, properly maintained, exceeds 30 years but it should be considered that during this time the demands for environmental performance will most probably become stricter. Hence, one will have to anticipate re-investments, retrofits and upgrading throughout the technical life of the plant.
The depreciation time is a legal/fiscal time that may or may not have a connection to the actual, technical life-time.
Limits to the combustion process
Any fireplace is designed to work best with a specific fuel at a specific firing rate (i.e. thermal output). Good combustion equipment fed with the correct fuel at the correct rate will provide a complete burnout of the fuel in combination with minimal amounts of air pollutants. This is especially important in case of individual house heating, be the houses large or small, with individual boilers. A cluster of buildings all emitting for example high concentrations of soot or heavy hydrocarbons may well cause the outdoor air quality to become a local health hazard. Also may nitrogen oxides be formed, and they, too, represent a source of air pollution.
As already pointed out in chapter 00-01, the combustion process is an intricate combination of aerodynamics, heat- and mass-transfer, and chemistry.
Not going into any detail, it might be clear that a small thermal output requires only a small fireplace and it might also be clear that if a single fuel particle occupies a large fraction of the volume in the fireplace, the combustion results will to a great extent be determined by the combustion of that single particle. Fundamentally, this is the reason that log-firing in single family houses may result in very high emissions of unburned hydrocarbons: The single fuel "particles" (i.e. wood logs...) will have variable properties and the single "particle" will occupy a significant amount of the fireplace volume. With wood pellets, the particles are uniform in shape and quality, they are comparatively small and the environmental performance of pellet combustion is far superior to that of common wood-log firing.
Now; for larger buildings, this is still true, but the fireplace is bigger than it is in the single-family application, and so is the thermal output. While the single-family house may accept manual stoking, the larger building will not, and hence wood-log firing is effectively out of question. Pellet firing can be automatized and lends itself excellent for the interval 50 1000 kW but might prove uneconomical. These are the reasons that wood-chips firing has found a niche in this segment.
The problems encountered with wood-chips in these scales are all basically due to the non-uniformity of the fuel in combination with the relatively speaking small fireplace volume. At the low end of the segment, 50-100 kW is the fireplace cross-section in the order of 50 cm while the single chip particle may be as big as 10 cm. At the same time will the individual chips particles exhibit very variable moisture content. Finally is the fuel feed in the smaller scales very sensitive to bridging and to mechanical disturbance. In the upper end of the segment, 700-1000 kW, are these circumstances of much less importance and a smooth and well-controlled combustion and operation may well be guaranteed, provided only that the boiler and the fuel feed system are properly designed.
Relevant standards
If not installed originally, retrofitting a building to a central heating system may represent a significant investment and it is important that the equipment bought fulfils all reasonable quality criteria. The European federal standard EN 303-5 (see the Forest StandardGuide) covers testing procedures and marking of boilers with a maximum heat output of 500 kW. Such boilers are in many cases suitable for use in this sector. Again, EN 15316-4-7 covers the dimensioning methods for building heating systems.
SELF TEST
This handbook, except for the four introductory chapters 00-00 through 00-03, is based on a matrix structure and can be studied either by column (= application) or by row (= fuel quality). Depending on how you choose to read it, the tests with the individual chapeters may become slightly different.
TEST what you have learnt along the row about applications in different scales!
TEST what you have learnt along the column about different fuels in larger buildings!
INTRODUCTORY CHAPTERS 00-00: Global resources 00-01: Energy fundamentals 00-02: Over-all biomass properties 00-03: Fuel/Energy supply | ||||
FUEL↓ APPLICATION→ |
SINGLE-FAMILY HOUSES | Download pdf | DISTRICT HEATING | COMBINED HEAT-and-POWER |
FIREWOOD Introduction Properties |
Domestic firewood |
NOT APPLICABLE |
NOT APPLICABLE |
NOT APPLICABLE |
PELLETS and BRIQUETTES Introduction Pellet properties Briquette properties |
Domestic pellets | Large bldng. pellets | DH pellets |
NOT APPLICABLE |
WOOD CHIPS Introduction Properties |
NOT APPLICABLE |
Large bldng. chips | Chips for DH | Chips for CHP |