05-02 Cost structure with herbaceous fuels
05-02-01 Elements important for the total fuel cost
Introduction [Robert R. Bakker and H.W. Elbersen]
In the bio-based economy, renewable herbaceous biomass such as straw and perennial grasses will become important cellulosic feedstock’s for conversion to biofuels, chemicals, electricity and heat. A significant fraction of this herbaceous biomass consists of inorganic constituents, commonly referred to as ash, which cannot be converted to energy. Not only the amount of ash, also may the composition be of great importance. Ash content can originate from the biomass itself or from collection and pre-treatment methods and often lead to high disposal costs resulting in a negative economic impact on biomass conversion systems. Only in a few cases and under certain conditions, such as thermal conversion of rice hulls have biomass ash residues become a marketable product. The negative impact of inorganic constituents in herbaceous biomass may be aggravated in biochemical conversion systems (such as production of cellulosic ethanol), where the use of inorganic chemicals during pre-treatment adds to the total amount of non-convertible inorganic residues in the conversion system.
In this segment taking reference to the regions across Europe defined in chapter 02-02 the two main areas for economic review are split into
a) Agricultural Residues
- Straw – by-product of arable farming.
- Olive Kernels – by-product of olive farming
b) Energy Crops
- Willow
- Miscanthus
By reviewing the economics of these four sources of herbaceous fuels it is anticipated that the majority of the costs will be dealt with on a percentage of total cost basis.
Agricultural residue (Wheat Straw) |
Woody-biomass (Willow) |
Switchgrass | Forage Sorghum (Grass) |
Bioenergy Sorghum (Grass) |
|
Biomass per acre per year (dry tonnes) |
2 | 7 | 8 | 10 | 15-20 |
Estimated cost delivered to converter ( € per dry tonne) |
45 | 40-50 | 50-80 | 55 | 40-47 |
A distinct difference must be noted in yields between energy crops and those that are established for other purposes that contribute to energy as a bi product in the form of agricultural residues. Wheat straw yields circa 8 t/ha in Ireland in grain and from table 2t/ha of straw, reference table 05-02 1. The straw element providing energy potential of only 25% of the overall produce should it enter the biomass fuel supply chain? Energy crops are established to yield 100% of the produce for sale as energy.
05-02-01a Elements of special importance with agricultural residues
Olive Kernels and residues - Agricultural Residue A (Mediterranean)
Low moisture (<15%) and relatively high heating values of dry pressed olive kernel
(23.7 MJ/kg) combined with locality in production and huge amounts make it an attractive form of agricultural residue for its local thermo chemical
treatment in decentralized, probably modular, small energy production systems. Olive kernels, at the moment, are exploited through conventional combustion
mainly from the same factories where they are produced, to cover their energy consumption needs, especially in drying processes.
Today, the cost of dried pressed olive kernel reaches 0.46 €/kg (while in 2001 it was around 1 €/Kg). But under conditions of international competition and problems of tracing amounts of benzopyrenes, (components that are assumed carcinogenic) in olive kernel oils of Spain, Italy and Greece, its value was affected and has reached the present prices, something that also entrained downwards and the price of olive kernels as a fuel. But still dry pressed olive kernel is utilised as an excellent fuel and in comparison with the present high petroleum prices (0.577 €/l) olive kernel cost is reduced almost 12 times (0.046 €/Kg).
[Agricultural residues for decentralized energy production, V. Skoulou, A. Zabaniotou]
Transportation Cost in Mediterranean Region (Italy)
1 tonne = 0.5 €/km including VAT for a distance < 50km
1 tonne = 0.4 €/km including VAT for a distance > 100km
Breakdown Cost of Olive Kernels
Purchase price 46 €/tonne
Assuming transport distance of 50 km at 0.5 €/km = 25 €/tonne
Total cost of dried pressed olive kernels with a transport distance of 50 km = 71 €/tonne
Alternative practices to collect biomass from olive tree pruning
Several possibilities (all of them including machinery costs) have been considered:
Estimated Cost €/tonne |
|
Olive tree residues cut in the processing plant | 36.97 |
Olive tree residues cut directly in field, by means of automatic machinery | 41.71 |
Olive tree residues cut directly in field, by means of manual machinery | 46.56 |
Olive tree residues cut directly in field, with highly efficient machinery | 31.13 |
Source: [Economic viability of the use of olive tree pruning’s as fuel for heating systems in a public institutions in South Spain F.J Lopez, S. Pinzi, M.P Dorado]
Straw – Agricultural Residue B (All regions)
Straw such as wheaten, barley and oaten straw is typically used as bedding and feeding for livestock it can also be used as a fuel source. The
establishment is categorised as zero as it is an agricultural bi-product. The fuel price associated with straw can be categorised into the following:
Elements of Supply Chain | per bale € |
per tonne € |
per GJ € |
Distribution % |
Cost of Straw on ground | 14.75 | 29.5 | 1.99 | 47.1 |
Price to bale* straw | 6.5 | 13 | 0.88 | 20.7 |
Price to collect and gather | 1.08 | 2.16 | 0.15 | 3.4 |
Price to return to holding depot | 0.75 | 1.5 | 0.1 | 2.4 |
Transport up to 50 km | 7.5 | 15 | 1.01 | 24.0 |
Brokerage | 0.75 | 1.5 | 0.1 | 2.4 |
Totals | 31.33 | 62.66 | 4.23 |
* based on a 500 kg bale with dimensions 2.4 x 0.9 x 0.9 m
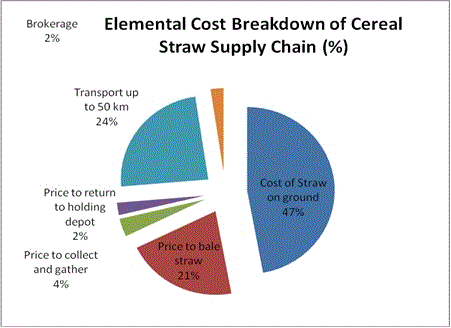
Figure 05-02 1: Cost distribution in cereal straw residue.
It is fair to deduce that the main cost is the straw itself but most interesting is that the transport equates to almost a quarter of the cost up to 50 km
radius from field. It would be a logical assessment to note that transport beyond 50km is not advisable.
05-02-01b Elements of special importance with energy crops
Willow – Energy Crop A (All regions except Mediterranean)
Cost of fuel is as per Chapter 02-01 as in principle they are supplying the same market in each region examined where produced. Distinct differences occur
in the establishment and harvesting of Willow from that of pulp wood/brash whilst having the same value per GJ delivered to fuel silo. In principle
pulpwood when reviewed is a agricultural bi-product as distinct to an energy crop specific for energy market.
The establishment of willow can be broken down to operational costs and material costs. These can be further sub divided as follows:
Elements in Supply Chain | Boreal (Swedena) |
Atlantic (N Irelandb) |
Continental (Poland) |
Establishment | 86 (17) | 159 (28) | 64 (27) |
Fertiliser | 93 (19) | 83 (15) | 39 (16) |
Harvest | 106 (21) | 140 (25) | 62 (26) |
Field transport | 33 ( 7) | 51 ( 9) | 12 ( 5) |
Transport to heat plant | 116 (23) | 106 (19) | 28 (12) |
Brokerage | 39 ( 8) | no data | 23 (10) |
Supervision | 17 ( 3) | 11 ( 2) | 3 ( 1) |
Cost of wind-up (Yr 22) | 5 ( 1) | 8 ( 1) | 2 ( 1) |
Weed control post harvest | 4 ( 1) | no data | 3 ( 1) |
Total Price Return for grower (€/ha/annum) |
499 | 558 | 236 |
Note: Willow is not typically grown in the Mediterranean region.
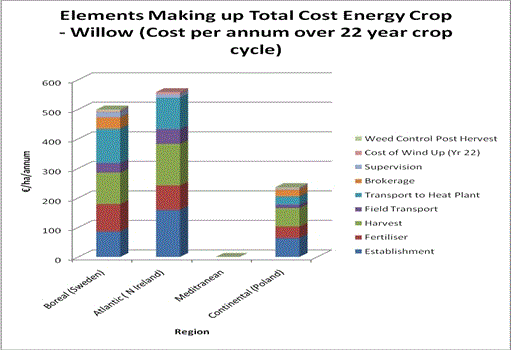
Figure 05-02 2:
Graphic of Elements that make up willow fuel cost
Reviewing the above figures and chart above it is clear that the returns from willow production for the farmer are not very attractive in years that traditional cereal crops price is high. High establishments cost of up to 28%, harvesting also accounts for a large cost up to 26%. In countries like Ireland the availability of planting and harvesting machinery is a big issue particularly when compared with the availability of cereal machinery.
As such over the 22 year cycle the major challenge is increasing the hectares of willow established. More focus might be directed to establishment in less productive lands but this will have an effect on the crop yield over that 22 year cycle.
Miscanthus – Energy Crop B (Continental and Atlantic)
Cost of fuel is as per Chapter 02-01 as in principle they are supplying the same market in each region examined where produced. Distinct differences occur
in the establishment and harvesting of Mischantus from that of pulp wood/brash whilst having the same value per GJ delivered to fuel silo.
Miscanthus has a net calorific value, on a dry basis, of 17 MJ/kg (4.7 kWh/ kg)) with a 2.7% ash content. Growing Miscanthus as a fuel is very energy efficient. A UK lifecycle energy analysis determined an energy ratio of over 30 for Miscanthus i.e. for every unit of energy expended in producing the crop over 30 units of energy are obtained.
Taking 0.137 GJ (3.8 kWh/kg) energy content at practical 20% moisture content then 1 tonne equates to 13.68GJ (3800kWh).
The establishment of mischantus can be broken down to operational costs and material costs. These can be further sub divided as follows:
Atlantic (UK) |
Boreal (Sweden) |
Continental (Germany) |
Mediterranean (Italy) |
|
Crop revenue (€/t) | 52 | 65 | 43 | 70 |
(€/ha) | 537 | 760 | 742 | 1270 |
Planting subsidy (€/t) | 0 | 0 | 0 | 0 |
Recurring subsidy (€/ha) | 0 | 0 | 0 | 0 |
Single farm payment (SFP) (€/ha) | 320 | 242 | 317 | 554 |
Total revenue (Crop+SFP) (€/t) | 83 | 86 | 61 | 101 |
(€/ha) | 857 | 1003 | 1058 | 1824 |
Total establishment cost (€/t) | 21 | 16 | 12 | 17 |
(€/ha) | 216 | 187 | 205 | 316 |
Total recurring cost (€/t) | 40 | 30 | 28 | 34 |
(€/ha) | 419 | 348 | 488 | 621 |
Total cost (€/t) | 61 | 46 | 40 | 52 |
(€/ha) | 635 | 536 | 692 | 938 |
Net margin (Without SFP, €/t) | -9 | 19 | 3 | 18 |
(€/ha) | -98 | 225 | 49 | 332 |
Net margin (With SFP, €/t) | 21 | 40 | 21 | 49 |
(€/ha) | 222 | 467 | 366 | 887 |
Costs are €/tonne wet yield (€/t) and €/hectare (€/ha)
This study of crop returns from Mischantus details that there is marginal return if any in the absence of the single farm payment subsidies provided at EU level. This is assuming that the crop is sold as wet yield at the farm gate.
Similar issues arise in the return for the farmer in Mischantus as discussed in Willow. The specific establishment cost below would in some cases require that the producer seeks finance to cover the large establishment costs and must wait a min of 3 years for its first crop.
Activity | Cost €/ha* |
Rhizome cost (using18000 rhizome per ha) | 1427.4 |
Cultivation | 101.26 |
Herbicides | 117.12 |
Contract planting | 366 |
Total | 2011.78 |
* Exchange rate £1=€1.22
Source: [Economics of Miscanthus and Short Rotation Coppice Production 2006]
Once the grower has made the commitment to establish the crop and waited the minimum 3 years for first harvest he/she must then be prepared for further large costs to complete the harvest. Be it chipped in field using traditional forage harvester technology or in the form of mowing and baling. This cost if carried out using baling mechanism can be less than the 28% discussed under willow section.
Activity | Cost €/ha* |
Mower conditioner | 24.4 |
Baling (@16% moisture content) | 134.2 |
Carting, stacking and loading | 48.8 |
Total | 207.4 |
* Exchange rate £1=€1.22
Source: [Economics of Miscanthus and SRC Production 2006]
Once the crop is at the farm gate it then must go through further processing phase to get the material to the fuel silo. Typical prices in Table 05_02 6
Operation in Miscanthus Fuel Production | €/tonne |
Price to grower | 48.50 |
Harvesting costs | 16.50 |
Haulage to fuel processing depot | 6 - 8 |
Shredding into fuel size | 7 - 10 |
Drying to 20-30 % MC | 5 |
Haulage to boiler | 6 - 8 |
Overhead and admin costs | 8 - 10 |
For Mischantus to become a viable enterprise for growers they will need to consider adding value to the material by drying it. Then by focusing on the sale as energy value in GJ as opposed to the traditional method of weight or volume. In selling as an energy value this may create higher returns when compared to the price of oil per GJ delivered. This all on the premise that the market for the fuel exists in the 50km vicinity of the crops location.
Taking all of the above costs into account this implies a cost of € 92 per tonne delivered to a silo at a biomass installation in the Atlantic region. This converted to energy value using conversion value set out earlier gives a value of €6.72 per GJ. This is in an Irish context is low and is seen as an unsustainable end price to allow market development. However if a higher price per GJ were achievable relative to increasing fossil prices then the market could grow subject to market demand.
A similar price may be assumed for Boreal region but one must note that there is little if no production in Sweden.
Summary of Total Fuel Cost:
Traditional land usage provides higher returns for farmers and as per previous case study where the farmers had a parasitic energy load drying a substantial volume of grain for food market. Taking into account the limited market for the produce the end price per GJ is not favourable.
To draw a conclusion from this it is that in regions where the heat market is small from biomass the likelihood is that lingo cellulose materials will lead the way to developing the market. Once the market strengthens and matures then the focus might have to shift to specific energy crops. This is borne out in the case studies presented with the exception where a farmer has a specific need like that in section 05_02_03b. In the interim the use of agricultural residues can assist the lingo cellulose material to develop the market and pave the way for specific energy crop production.
05-02-02 Elements making up the total system cost
The total system costs for the herbaceous fuel sources are almost identical to that of the ligno cellulose ones described in text section 05-01-02. It is importunate to note that the higher chlorine content of miscanthus and straw dictate that a more robust combustion chamber may be required in the event of super heated systems Refer to Chapter 02-02, thus increasing the initial cost, although the combustion of miscanthus and willow remains feasible where the macro economics discussed in chapter 05-01 allow.
UK London City 1060 MJ |
Ireland (Case study 3b) 1090 MJ |
Slovenia (Example) 2300 MJ |
|
€ | € | € | |
Feasibility Study | 3 152 | 1 000 | 7 000 |
Development | 3 152 | 0 | 28 000 |
Engineering | 5 516 | 0 | 105 000 |
Heating system | 117 314 | 159 950 | 995 600 |
Balance of system & misc | 17 421 | 5 400 | 215 130 |
Total | 146 555 | 166 350 | 1 350 730 |
Using the provided cost tables and explanations a designer may provide some useful information to a heat user that is considering implementing a small, medium or large scale biomass heat plant or heat network on potential capital and operational expenditure.
05-02-03 FEASABILITY STUDIES
05-02-03a Straw Fired Biomass CHP Plant Midleton Co. Cork Feasability Study
A proposed 18 MW straw fired biomass combined heat and power plant in Middleton Co Cork is expected to produce 144 GWh of clean electricity and 284 GWh of clean heat annually. The plant is expected to consume 110 000 tonnes of straw annually at a moisture content of 15%. The straw will be supplied from local agricultural industry. The estimated cost of the straw in 20-25 €/tonne to the producer which equates to 50-55 €/tonne delivered to the plant. Potash is a by-product of burning straw which is rich in potassium and phosphorus. This by-product can be resold to the farmer at a cost of 40 €/tonne.
Summary:
Capacity: 18 MW Straw CHP Plant
Output: 136 000 MWh per annum
Revenue: € 14.7 million estimated Year 1
Project Cash Flow: € 5.9 million estimated Year 1
Capital Costs: € 49 million from supplier indications
Project Payback: 6.7 Years
Project Return: 13%
Equity Return: 19 %
Base Assumptions:
Power sales at estimated (PES) € 0.108
Likely straw cost range € 50-55/tonne: € 55 (€ 0.048 per kWh) has been used in the example
70% Debt 15 Years
Does not include tax incentives
€ Million | % | |
Straw Boiler/Fuel handling and Cooler | 27.9 | 57 |
Turbine | 6.6 | 13 |
Building, Elec and Mech | 7.5 | 15 |
Design and supervision | 4 | 8 |
Capital interest | 3 | 6 |
Total | 49 | 100 |
€/kWh | % | |
Electricity price | 0.108 | 100 |
Margin | 0.046 | 42.6 |
Straw Cost | 0.048 | 44.4 |
Other Cash Cost | 0.014 | 13 |
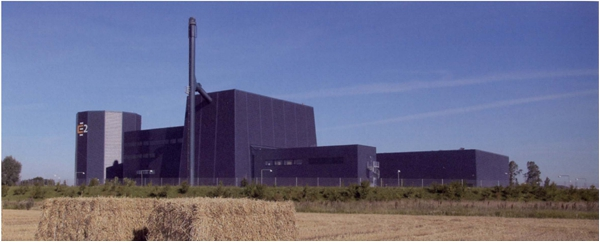
Figure 05-02 3: Straw Fired CHP Plant Middleton Co Cork – Modelled Image
05-02-03b Multi Fuel Energy Cabin Ardee Co. Louth
At Ardee in Co. Louth, the McGuiness brothers have an energy cabin installed. It is the first of its type in Ireland, and will future proof their farm from rising energy costs. The energy cabin is fully automatic in operation, combining free energy from the sun with a renewable biomass boiler that can burn wood chips, various grain crops, nut shells, hemp and even straw. The heat produced will be used to dry grain and wood chips harvested on the farm. Twenty ha of willow is grown on the farm.
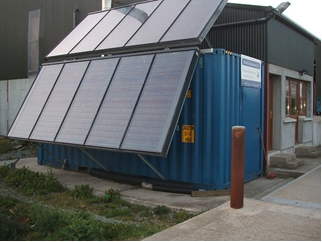
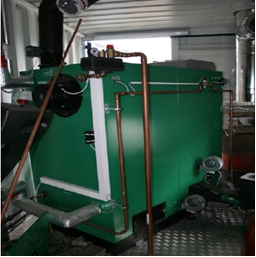
Figure 05-02 4a, b: Energy Cabin with solar thermal panels.
The energy cabin (a converted container) consists of a 130 kW multi fuel boiler and 24 m2 of solar panel which brings the output up to 150 kW. The heat is stored in 1500 litre hot water accumulator tank. The hot water is then pumped through highly insulated piping to a heat exchanger in front of two 30kW fans, which in turn force hot air through the ventilated floor of the drying shed refer to Fig 05-02 6. Grain, willow and other crops can be dried in this shed reducing their moisture content by 12 – 15%.
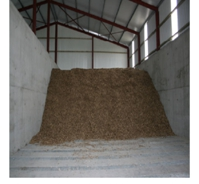
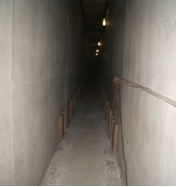
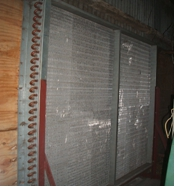
Figure 05-02 5a, b, c: Drying Shed with Ventilated Floor and Wind tunnel with air to water heat exchanger at one end.
By using a renewable energy crop produced locally on the farm for these processes, the McGuiness’ brothers are not only cutting their drying costs of their cereal business by two thirds but they are also greatly reducing their carbon dioxide emissions which contribute to global warming. Biomass boilers are classified as carbon neutral in that the amount of CO2 emitted in burning is no higher than the amount of CO2 which the fuel would have absorbed during growing.
Costs
As the grain store and drying facilities were built on a green field site the cost were quite substantial:
• Equipment and installation related to the grain drying: €120 000
• Shed, floor units and drying facility: € 450 000
• The project was eligible for a 50 % grant which was provide by Interreg 3A RENEW project.
The system was expected to displace 30 000 litres of diesel drying 4 000 tonnes of grain, but due to the wet harvest experienced in 2008, 40 000 litres of diesel was saved. Using willow grown on farm an estimated € 17 000 is saved in drying costs.
The McGuiness’ have secured a contract to supply and dry willow commercially for a briquette factory 20km away that are producing briquettes.
The original break even pay back (Refer to Chapter 05_00) was expected to be seven years compared to a conventional diesel based drying unit. Due to the wet harvest and the high price of oil this was reduced by almost two and a half years.
05-02-03c Growing Willow on Contract Feasibility Study (Ireland)
There has been some study completed on the feasibility of a farmer growing willow on contract in Ireland based on a 10 year outlook to allow one to compare it to the more common practice of grain or grass production.
To describe the table one must understand the life cycle of an energy crop like Mischantus or Willow where there is not an annual harvest.
This table sets out all the costs and projected cash flow returns.
Biomass Project - 10 Year Outlook (Cash Items) - Farmer Growing Willow on Contract (Ireland) | ||||||||||
Year 1 € |
Year 2 € |
Year 3 € |
Year 4 € |
Year 5 € |
Year 6 € |
Year 7 € |
Year 8 € |
Year 9 € |
Year 10 € |
|
COSTS per hectare | ||||||||||
Cultivation | 150 | |||||||||
Planting | 400 | |||||||||
Planting stock | 1 600 | |||||||||
Spray (herbicide/insecticide) |
250 | |||||||||
Fertiliser | 150 | |||||||||
Cut back | 100 | |||||||||
Rabbit Wire | 150 | |||||||||
Herbicide | 75 | 50 | 50 | |||||||
Reclamation costs | 400 | |||||||||
Harvest and Chip | 500 | 500 | 500 | |||||||
Drying cost (€5 per tonne) |
150 | 150 | 150 | |||||||
Operational Costs | 2 900 | 75 | 0 | 650 | 50 | 0 | 650 | 50 | 0 | 1 050 |
Establishment Aid (50 %) |
-1 088 | -363 | 0 | 0 | 0 | 0 | 0 | 0 | 0 | 0 |
Costs before financing | -1 813 | 288 | 0 | -650 | -50 | 0 | -650 | -50 | 0 | -1 050 |
INCOME per hectare | ||||||||||
Sale of harvest (@ €80/tDM by 12 t/ha/annum) | 2 088 | 0 | 0 | 2 088 | 0 | 0 | 2 088 | |||
Energy payment | 125 | 125 | 125 | 125 | 125 | 125 | 125 | 125 | 125 | 125 |
Total income | 125 | 125 | 125 | 3 005 | 125 | 125 | 3 005 | 125 | 125 | 3 005 |
Net income before Financing | -1 688 | 413 | 125 | 2 355 | 75 | 125 | 2 355 | 75 | 125 | 1 955 |
Closing (Deficit/Surplus) |
-1 688 | -1 275 | -1 150 | 1 205 | 1 280 | 1 405 | 3 760 | 3 835 | 3 960 | 5 915 |
In light of this study the business case at present as discussed for productive lands in Ireland is not strong at €591/ha per annum in year 10 having suffered much lower returns in years 1 -9.
Useful Links:
A number of case studies are available at the IEA task-38 page: http://www.task38.org
Some dedicated energy crops – like miscanthus – may be locally profitable and in some cases on-line calculators are available.
References
- Robert R. Bakker and H.W. Elbersen Manging Ash Content and -Quality in Herbaceous Biomass:An Analysis From Plant to Product
- Agricultural residues for decentralized energy production, V. Skoulou, A. Zabaniotou
- Market for Olive Residues for Energy 2008 Intelligent Energy Europe
- Economic viability of the use of olive tree prunings as fuel for heating systems in a public institutions in South Spain F.J Lopez, S. Pinzi, M.P Dorado
- Karin Ericsson, Håkan Rosenqvist, Ewa Ganko, Marcin Pisarek and Lars Nilsson An agro-economic analysis of willow cultivation in Poland
- Miscanthus as an Energy Crop and its Potential for Northern Ireland Agri-Food and Bioscience Institute
- Economics of Miscanthus and SRC Production 2006
- Bioenergy Strategy and Action Plan for the Mid West Region
- Rural Generation