00-01: What is energy and why do we need it?
Energy is a prerequisite for modern, western style life. For many people, energy is equal to electricity but that is not true: Energy is a natural entity that can take many forms but common to all the forms is that energy is something that can be used to perform work. Work can be to change the shape of something, to change the position of something, to change the properties with something like changing its temperature or pressure or density or to change the state of aggregation of something like melting or vaporizing.
So energy is used to maintain a comfortable indoor climate warmer or colder than outside and it is used to preserve food in the refrigerator or in the freezer as well as to cook the food, it is used to run cars and bicycles, it is used to maintain the body temperature, to run computers, in bonfires. It is used to produce steel and glass and ceramics, to pump water, if you are a scuba-diver it is used to fill your air tubes with compressed air...
So energy is a natural entity and it has the fundamental property that it cannot be created nor destroyed. Energy can only be changed, and the change will always lower the quality of the energy. However, we shall sometimes use the everyday phrasing of "energy production" and "energy consumption" throughout this material though it is not thermodynamically correct.
What is energy used for and what is the need?
The present material is restricted to the use of energy in buildings and the supply of energy to buildings. In
buildings, energy is used mainly for the following purposes:
• Illumination and home electronics. For this, electricity is the only alternative.
• Food preparation and preservation. For this, electricity is the most common energy carrier but
fossil gas, propane or kerosene can also be used and are so in some of the European states.
• Hot tap water. For this, there are several alternatives: Hot tap water can be produced in
gas-fired water heaters, in electric water heaters, by domestic boilers fired with gas, oil, coke, kerosene or
biofuel, or it may be provided by district heating systems, fired with most any fuel.
• Space heating and cooling. Again, there are several alternatives domestic boilers, electric
systems, gas-, oil-, propane-, pellet- or kerosene stoves, district heating, district cooling...
The proportions between these four uses vary between different latitudes, different seasons and different types of buildings.
What you will notice is that there is no need for energy as such but for the energy services that can be provided. An energy service like a comfortable indoor climate can be produced locally starting from an energy carrier. Energy carriers are of many different kinds: electricity being the most refined one while fossil gas, gasoline, propane bottle gas, biofuel, coal, oil and all other ones are less sophisticated.
For the end user, electricity is among the most comfortable energy carriers. For the end user, electricity is clean, it is simple to control and it is in most places easily available. However, from a production and a system point of view, electricity is not always the best alternative.
Strictly thermodynamically speaking, electricity is the most high quality energy carrier and hence it is also the one that is most difficult to produce. This is a fundamental property and means that thermal energy can only partly be converted into electricity. Therefore, electricity production in fuel-fired, condensing power stations, which is so far the most common in Europe, implies huge losses of energy. In top-modern gas-fired combined-cycle power plants may the losses be just below half the energy input while in more old-fashioned coal-power plants the losses may well exceed 60% of the total energy input so that only about 40% of the input energy actually becomes electricity. In nuclear power plants, the losses are even bigger.
So for an energy system to be efficient in the total sense, the use of electricity should be restricted to such applications where it is the only or the by far best alternative. For buildings, this means that electricity should be used for illumination, for home electronics and for food preparation and preservation but not for tap water or for climate control.
The ideal situation, the situation that would provide the best opportunities for an efficient energy system in total, is the one where the total delivery consists of ratio electricity to other energy carriers, which is equal to the consumers needs of electricity and of other energy carriers.
Looking back to the four main needs for energy, and assuming that electricity is used for light, for home electronics and for food handling, we may state that the need for electric power is not too variable throughout the year. The need for light is of course larger during the dark season but with modern, low-energy illumination the dominant electricity demand is switching towards electricity for cooking and food preservation together with electricity for computers, TVs and other home electronics. And this need is not so very seasonal.
The need for tap water is also not too dependant on season but is similar in winter, in summer and in between.
The energy need for climate control though is extremely seasonal with a demand for heating during winter and a demand for cooling during summer and sometimes during the year no demand at all. This is of course very much dependant on latitude and on local climate but just for reasoning purposes, one may assume the following.
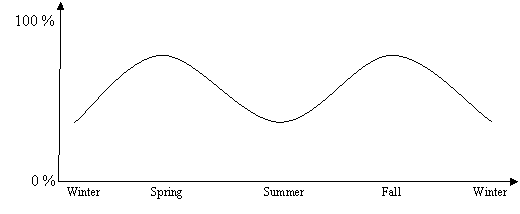
The schematic illustrates how the relative need for electricity in a fictitious case is low in winter because of the large need of heating energy and in summer because of a large need for cooling, while the relative need for electricity is high during spring and fall because then the need for climate energy is low and the only need for other energy than electricity is to produce tap water.
The role of the energy supply system is then to supply the customers with the correct mix of energy carriers throughout the year and the role of the city and energy planners is to plan the buildings to use the correct type of energy carriers for the correct purpose.
What are the production options?
The everyday word "power station" denotes an industrial plant where water is boiled to steam and the steam is used to run turbines which in turn are connected to generators. The water may be boiled using coal, nuclear fuel, waste, biomass, gas, oil or anything else.
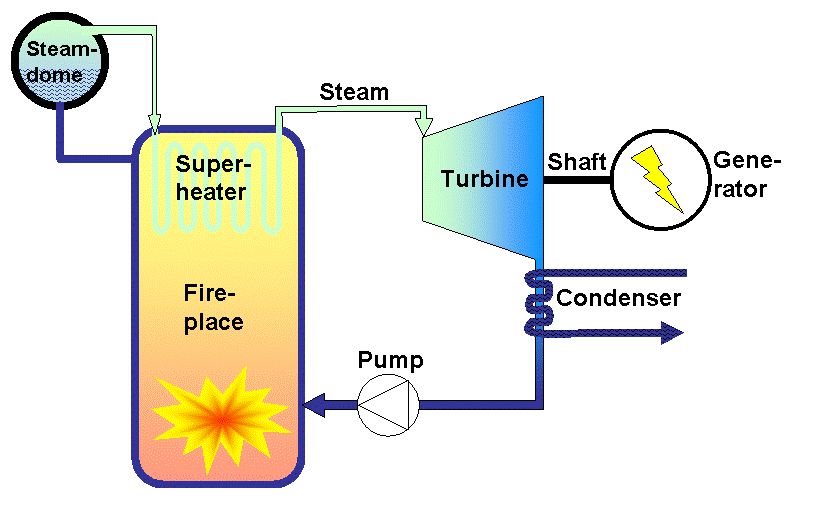
If the power plant is of the "combined cycle" type, then the fuel is first burned at an elevated pressure and the high-pressure gases pass a gas turbine before they enter the steam-raising device. So in a "combined cycle" plant there are both gas turbines and steam turbines.
For the highest possible efficiency with steam turbines, the steam temperature and the steam pressure before the turbine should both be as high as possible and the corresponding values immediately after the turbine as low as possible. Hence, condensing power stations, as they are called, use ambient air in cooling towers or they use sea water or cold water from nearby rivers as cooling media in the condenser.
The CHP concept
As mentioned, high steam pressure and temperature at the turbine inlet, combined with the lowest possible pressure
and temperature at the turbine outlet, are the prerequisites for high conversion efficiency. The drawback with this
is that the outlet water temperature becomes close to ambient and that the energy loss, i.e. the cooling medium,
cannot be used.
If the restrictions for the turbine outlet conditions are eased and a higher temperature of the cooling water is accepted, then the cooling water may become a valuable side-product. This is the concept of combined heat and power production, CHP. A CHP-plant will work with condenser temperatures in the range of 40-80 °C while a condensing power plant will use temperatures in the range from 5 degrees to ambient. The electric efficiency of a CHP-plant is thus restricted to about 38-40% but since the side product is district heating may the total efficiency well exceed 90%.
A CHP-plant may thus deliver a product mix with a maximum ratio of electricity/heat about 80% and this ratio is adjustable so that the proportion of heat can be increased.
Cooling production from heat!
Except electricity, the fictitious customer was supposed to have a need for space heating during winter. Also,
there was supposed a year-around need for hot tap water. But during summer, it was assumed that the need was for
cooling not for heating.
Cooling is a complicated process but one may state that if there is a cold medium available inside a building, then that medium can be used to lower the temperature of the indoor air by fanning the air through a heat exchanger cooled by the cold medium.
In the most common air conditioning units, electricity is used to produce a cold medium in a compressor cooling machine. The cooling factor for such compressor units is about 3-4, meaning that to cool away one unit of energy you have to supply about 0.25 0.3 units of energy in the form of electricity. Hence, cooling by compressor cooling machines will consume electricity from a system point of view.
The other option is to use absorption cooling machines instead of compressor cooling machines. Absorption cooling uses only very minor amounts of electricity, but the main energy supply to the unit is instead in the form of heat. Absorption cooling is widely used in propane-fired refrigerators used in caravans or for food preservation in remote areas. Since heat regarded from a pure thermodynamical standpoint has a much lower quality than electricity, the absorption coolers need very much more energy and the cooling factor is only about 0.5 or 0.6. To cool away 1 unit of energy you then have to supply about 2 energy units in the form of heat at about 60-90 °C. But if this heat is produced in a CHP-plant you will also have the chance to produce electricity. Hence, cooling by absorption cooling machines will produce electricity from a system point of view.
To summarize this:
If there is a need for heating, you may always produce electricity at the same time provided you use CHP-technology.
If there is a need for cooling and if you use absorption cooling machines, then you may provide the cooling by aid
of heat and then again you may produce electricity if you use CHP-technology for the heat production.
Since heating and cooling are basic needs in all buildings, you can always plan the energy system so that the heat
demand and the cooling demand provide the basis for electricity production.
The economy of scale and the quality of the fuels
To get a further understanding of the energy supply system, one has to be familiar with some fundamentals of the economy associated with the area.
First one has to define two fundamental terms, namely the fixed cost and the variable cost. In close
connection to these, two other terms will occur, namely the total cost and the specific cost.
• Fixed costs for an energy apparatus or for any machine are the costs that are
associated with the purchase, spread out over the life. Assume for example that you have bought an electric air
heater, a fan with a heating coil, and that you paid 50 for it. Assuming the fan will last five years we may then
attribute a fixed cost to it at €10/year.
• Variable costs are such costs that occur only when the machine is in operation. Assuming
the price for electricity at €0.15/kWh and that the fan has the heating power 1 kW (the motor is disregarded
in this example), the cost for electricity will be €0.15 every hour the fan is in operation.
• If the fan is used only 1 h/year, the total cost that year will be €10.15/year,
where €10 is the fixed cost and €0.15 is the variable cost. If the fan is used 100 hours over one year,
the total cost becomes € 10 + 100.0.15 = €25/year.
• The specific cost is the total cost divided by the total volume produced. Use the example
from the previous paragraph: in the first case, the fan is used only 1 hour/year, the total cost is €10.15 and the
total heat produced is 1 kWh. Hence that single kWh of heat costs €10.15. In the second case, the total production
was 100 kWh and the total cost was €25. Hence, the specific cost in this case becomes €25/100 kWh = €0.25/kWh.
The single-family household is in many cases sensitive to fixed costs since they represent a long-term obligation that cannot be influenced while variable costs may be changed from month to month by a change in private behaviour. Therefore, when the energy supply system for single-family houses is planned it is often most crucial that the total investment cost is as low as possible. This, in turn, means that the system has to be technically simple and that, in turn, implies simple-to-use energy carriers. Even if the specific cost, i.e. the consumer price, for gas as bought from the grid is high, may the low investment cost still be sufficient to convince the buyer to accept the installation of gas heating.
A wood pellet heating system will be more complicated and will cause a higher investment (fixed cost) but depending on the price for pellets may the total cost still become lower.
The situation is illustrated by the diagram below:
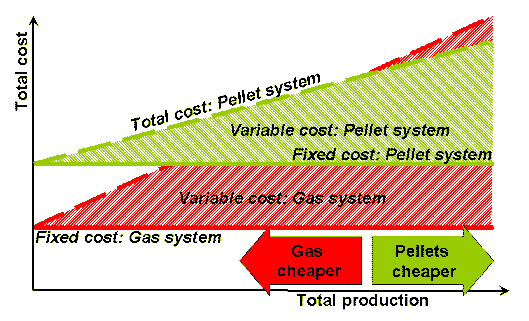
You will notice how in the diagram the low investment cost for the gas based system (red) renders the total cost to be lower for the gas heating system as long as the total energy consumption per year is low enough. At some specific, total, annual energy consumption will the pellet system become the cheaper one, because the low variable cost becomes the determining factor.
This is general:
• Large production units may carry high investment costs as long as the fuel is cheap and/or the variable costs are kept low by other means.
• Small production units may carry high variable costs if only the investment can be kept low.
To maintain a low investment cost in a fuel-based energy system in a single house, the fuel must be simple to handle. This is because the fuel feed system may come to include several mechanical devices like motors, screws, dosing equipment and also a separate control and safety system. Hence, fuel storing and fuel feeding does often represent a significant part of the total investment.
The second major part of the total investment in the single house is the internal system in the house to distribute the energy between the individual rooms. There are mainly two types of heating systems available namely air-borne systems and water-borne systems often referred to as central heating.
With air-borne systems, a fuel-fired device (stove) is used to heat up the air inside the building to a comfortable temperature and the warm air is then distributed. Modern stoves be they gas-fired, kerosene-fired or pellet-fired are designed so that they are actually almost pieces of furniture and they are easily integrated in common living-rooms. The advantage with this type of systems is the simplicity as long as the building interior allows for a simple heat distribution. The disadvantage is that the system is difficult to control with respect to the temperature in individual rooms and that it requires a separate system for hot tap-water production. For a house with a slightly more complicated interior where the distribution of warm air may be hindered may the air-borne system require several stoves to deliver the desired level of comfort. In such cases obviously will the investment cost increase radically.
With central heating, a fuel-fired device (boiler) is used to heat up water which is then distributed through a piping system to radiators in the individual rooms. Each radiator will be equipped with its own thermostat so that the temperature in the individual rooms can be set. The main advantage with this system is its controllability and the second advantage is that the same boiler can also provide the hot tap water desired.
The alternative to an individual boiler is to connect the central heating system to a district heating network. In this case, the boiler is replaced with a heat exchanger with double coils: one to produce the hot water for the radiators and another one to produce the hot tap water. A modern heat exchanger is a compact device and can be placed most anywhere in the house without disturbing the general impression. The interior distribution of hot water from the heat exchanger to the radiators is fully analogous to the interior distribution from the hot-water boiler.
Obviously, the investment cost for an air-borne system is often lower than for a central heating system but the level of comfort in combination with the fact that tap-water production is integrated in the system still makes central heating competitive.
It shall now be clearly stated that this handbook omits the alternatives based on electricity, on geothermal heating systems, solar heating systems and heat pumps. The main aim with this handbook is not to provide a complete installation guide but to outline the characteristics of biofuel-based energy supply systems in general terms.
Looking now at the fuel alternatives for air-heating systems, one may state that:
• Gas of a uniform quality delivered from a pipeline is the simplest fuel of all and the same thing can be said for heat deliveries through district heating. The only thing needed is basically a pipe, a valve and some kind of ignition device. For district heating, the ignition device is not needed, but a heat exchanger is. For now, the comparison is dealing only with the technical minimum and any kind of safety installations are disregarded.
• Gas of a uniform quality delivered from a bottle is slightly more complicated. In this case, a storage cabinet of some kind is added to the situation above.
• Kerosene-fired stoves would be the next, competing with wood-pellet fired stoves with an internal pellet store in simplicity.
Central heating systems with individual boilers will typically require that one room is dedicated as the boiler room while central heating with a district heating network and heat exchangers does not. Neither does the heat exchanger require a chimney. There will also be a need of a fuel store unless the boiler is gas-fired with gas from a pipeline system.
Again looking at the fuel alternatives for central heating, one finds that:
• Gas of a uniform quality delivered from a pipeline is the simplest fuel of all and district heating is the competitor.
• Gas of a uniform quality delivered from a bottle is slightly more complicated. Just as above, a storage cabinet of some kind is added to the situation above.
• Kerosene- or oil-fired boilers would be the next, competing with wood-pellet fired boilers in simplicity. In case the system is also equipped with an accumulator tank, solar heating can easily be incorporated. However neither kerosene or oil, nor pellets, require an accumulator tank to provide the best indoor comfort.
• Solid fuel with a manual feed such as traditional wood-log firing or coke firing will generally require an accumulator tank to even out daily variations in indoor temperature, but they may provide an alternative for the heating of single-family houses if the fuel is cheap enough.
• In larger units, wood chips become an alternative. The fuel feed system for wood chips becomes very complicated because the chips tend to stick together, clog, and may form vaults, they may freeze during winter and, generally speaking, they are a complicated fuel. Hence, wood chips, having a low variable cost, will take a high investment cost and are best suited only for lager scales.
To conclude, there is no fuel that can compete with pipeline gas in simplicity and in low investment cost but the price paid is the comparatively high fuel cost, i.e. the high variable cost. District heating will have a higher investment cost but is the main competitor.
The second simplest is bottle gas, again characterized by a low fixed cost but with a high variable cost.
The third simplest fuels are wood pellets and kerosene or oil, both of which can be used for air heating and for central heating.
In northern latitudes Scandinavia and in mountainous climates Austria has the domestic use of pellets for individual house heating expanded rapidly over the last few decades since the mid 1980s. In these countries, central heating is commonly installed in single-family houses and a large proportion of the pellets are consumed in pellet-fired hot-water boilers with a thermal power from 10-50 kW. At the same time, there have been more and more models of small scale pellet stoves, sizes 3-7 kW, for air heating introduced on the consumer market. So today, robust, reliable, cheap and smartly designed pellets stoves are one main alternative for complementary heating at any latitude.
In larger buildings such as hospitals, shopping- and/or sports centres and alike, may wood chips firing be an alternative. The smallest scale where wood chips become viable is about 100 kW thermal power but that is only the lower limit. The high investment costs for wood-chips handling in combination with the low cost for the fuel make chips firing the main alternative for district heating plants and for CHP-plants but not for the individual house.
Central and decentralized production
The energy supply to a cluster of buildings may be planned according to any of two completely different strategies:
• Fuel distribution in combination with a de-centralized (i.e. individual) energy production.
• Centralized energy production in combination with energy distribution.
The first option requires that the individual house is equipped with its own boiler or stove and this means that each unit becomes small (typically less than 25 kW thermal power). The main fuel alternatives in this small scale, as seen above, become gas, kerosene and wood pellets. The small scale at each unit will effectively prohibit cooling production or CHP so the individual units become "pure" heat producers and they will have no effect on the electricity balance. The good thing with this system solution is that as long as the fuel supply works it is robust. The bad things are that this system cannot be the basis for electricity production, it cannot be the basis for cooling production and it will not contain any advanced environmental control.
The second option opens up for a larger production unit, maybe large enough to be viable for electricity production using CHP-technology, maybe large enough for cooling production but definitely large enough for a sophisticated combustion control system and a more advanced environmental control. This type of system solution becomes more sensitive to disturbances than the prior one since there is basically only one production unit and only one distribution system and if any of these fails However, long time experience proves that the reliability is extremely high and that the system can be planned so as to be sufficiently robust to meet also the strictest demands. In Sweden, district heating systems based on hot water have been used since the 1940s while steam-based district heating systems were installed in the USA already during the 1870s.
The crucial factors for district heating and district cooling networks to be viable are the line load and the heat density:
The line load is defined as the total amount of energy delivered through the network during a specific period of time, typically one year, divided by the total length of the network in meters. The unit then becomes energy/time*length, for example MWh/year*m.
The heat density is defined as the total demand for heat energy for a specific period, typically one year, divided by the area that the houses to be supplied cover. The unit then becomes energy/time.area, for example kWh/h*m2.
Just to indicate some numbers the district heating systems in former East Europe do often have line loads well in excess of 20 MWh/year*m while the Scandinavian district heating networks will have average line loads less than 5 MWh/year*m, sometimes as low as 1.
In areas where the heat density exceeds approximately 20 kWh/year*m2 district heating should definitely be considered a main alternative.
Resilience, redundancy and flexibility
Meteorologists agree that the current climate change can be summarized in that the future weather will be warmer, wetter and wilder. The frequency of extreme weather events be it heat waves, floods, storms, cold periods or extreme rainfalls will increase while at the same time the global mean temperature will increase.
The scenario calls for caution when the basic infrastructure in society like the energy supply system is planned. The over-all climate trend warmer will call for a successively increasing demand for climate cooling and the energy infrastructure needs be planned to meet this. On the other hand will wilder weather conditions including the possibility of sudden very cold periods call for a system that can also deliver heat at rates higher than before. Finally may the wilder conditions introduce disturbances such as failures in the national electricity grid because of storm fellings or sudden stops in fuel delivery system because of flooding of roads.
New energy structures need take these facts into account and be planned with due caution to the resilience of the system, its capacity to stand disturbances. The first and most crucial thing for this is to base the system not only on one fuel but to plan for flexibility and to base the system not only on few central production units but to plan for a distributed production based on several smaller units instead.
There will also have to be a certain redundancy built into the system an over-capacity with respect to the product mix. In case of a sudden heat-wave, it must be possible to adjust the product mix to a larger proportion of cooling while when the weather becomes extremely cold, there has to be the possibility to switch the production into a larger proportion of heat.
The crucial factor for an energy system planned for our future weather conditions is thus the flexibility built into the system flexibility with respect to fuel and to production. The concept of combined heat-and-power production and district heating, in combination with absorption cooling, fired with locally produced biofuels in a number of smaller units is a natural and obvious part of such a system.
The combustion process and the environment
Any fireplace be it in a boiler or a stove is designed to work best with a specific fuel. Good combustion equipment fed with the correct fuel at the correct rate will provide a complete burnout of the fuel in combination with minimal amounts of air pollutants. This is especially important in case of individual house heating with individual boilers. A cluster of buildings all emitting for example high concentrations of soot or heavy hydrocarbons may well cause the outdoor air quality to become a local health hazard. Also may nitrogen oxides be formed, and they, too, represent a source of air pollution.
As a wet fuel particle is exposed to the hot environment in a combustion chamber, the first thing that happens is that it starts drying. With large particles like logs does the drying successively proceed through the particle from outside in, so that the central parts of the particle are still wet while the outer parts are completely dried. With small particles like in wood powder combustion does the drying occur more or less homogenous.
After drying does pyrolysis (degasification or devolatilization) start. During pyrolysis, tar, heavy hydrocarbons, carbon monoxide and other combustible gases are formed and released from the fuel particle. Again, in a large particle can this process be finished in the outer parts before it has even started in the centre while in smaller particles it may occur almost simultaneously in the whole particle.
The pyrolysis gases ignite already during the ongoing pyrolysis process and the heat released from the gas flames will support the pyrolysis and at the same time further heat the particle.
Finally once the pyrolysis has come to an end does the solid residue, the charcoal or the char, ignite and burn, basically without flames.
With biomass fuels is approximately half the energy released from gases while approximately half the energy is released from solid phase combustion.
Thus, since all biofuels finally burn in the form of char, the final temperatures attained in the solid fuel bed are similar for all types of biofuel. And these temperatures are high enough to produce glass, cast iron, ceramic brick and cement as proved by the fact that wood fired furnaces were used to produce the brick and the cement used to build the coliseum, to produce the mirrors in the mirror gallery in Versailles, to produce the cannons used at Waterloo, just to mention a few examples.
Gas phase emissions and unburned hydrocarbons
The temperature during the gas combustion, though, is lowered by the water vapour escaping from the drying zone and
may be as low as 7-800 °C. At such low temperatures are the chemical reactions slow and too moist fuel may result in temperatures low enough to effectively hinder the burnout of heavy hydrocarbons.
The successive stages during the combustion process will in combustion chambers with a continuous fuel supply occur all at the same time but in different places in the combustion chamber and then may the mixing of the different gases be insufficient. In such cases can the emissions of unburned hydrocarbons from biofuel fired units be significant. The reason can thus either be too high moisture content in the fuel or too bad gas phase mixing.
In other types of equipment namely such that operate with fuel batches will the different stages of the combustion occur in sequence, but in the same place. In these cases may the intensive pyrolysis after the initial drying lead to emissions of hydrocarbons because of the relatively low temperatures in combination with a high gas flow.
At the end of the combustion process, the combustion of dry charcoal, will the temperature be very high but the gas flows are low and hence the mixing may be insufficient. Thus, also during the last phases of batch combustion, may the concentrations of unburned carbon monoxide and hydrocarbons be high.
The combustion chamber will be dimensioned to work at specific thermal loads (kW/m3) and at specific moisture contents (i.e. heating values). Hence, changing the fuel quality from for example moist wood chips to again just as an example dry pellets or vice versa, will radically change the combustion temperature and will affect the environmental performance. The same thing also happens at overload or too low load.
Therefore, it is crucial that already at the planning stage the size of the combustion plants are chosen in close connection with an investigation of the fuel resources so that the individual plants can be supplied with the correct fuel qualities.
TEST what you have learnt!
INTRODUCTORY CHAPTERS 00-00: Global resources 00-01: Download pdf 00-02: Over-all biomass properties 00-03: Fuel/Energy supply | ||||
FUEL↓ APPLICATION→ |
SINGLE-FAMILY HOUSES | LARGER BUILDINGS | DISTRICT HEATING | COMBINED HEAT-and-POWER |
FIREWOOD Introduction Properties |
Domestic firewood |
NOT APPLICABLE |
NOT APPLICABLE |
NOT APPLICABLE |
PELLETS and BRIQUETTES Introduction Pellet properties Briquette properties |
Domestic pellets | Large bldng. pellets | DH pellets |
NOT APPLICABLE |
WOOD CHIPS Introduction Properties |
NOT APPLICABLE |
Large bldng. chips | Chips for DH | Chips for CHP |